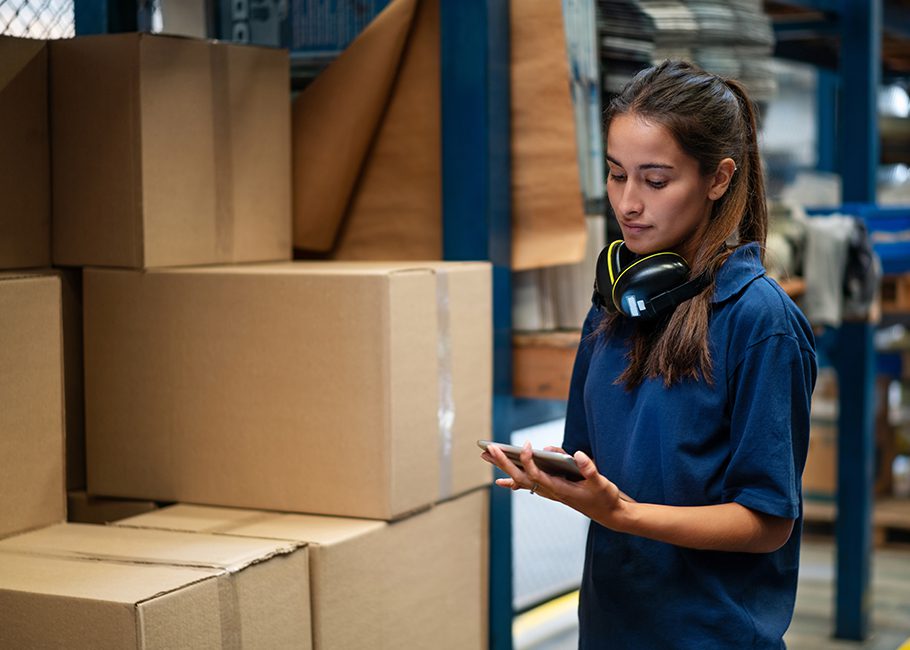
Imagine that your box setup machine has been operating normally. A recently delivered bundle of corrugated boxes is fed into the machine, and it immediately jams up. After a small amount of downtime, the machine operator clears out the machine and resets it. Once again, the corrugated is fed in. And, once again, the machine stops with the same error. Where does the problem lie? With the machine and/or its operators? Or with the boxes?
At PCA, our Performance Packaging Group (PPG) finds the solution to such problems—or, in a word, troubleshoots. PPG technicians have decades of experience buying, selling and maintaining box setup equipment, including case erectors, packers, sealers, etc. They know the common problems that lead to underperformance or failure in machinery and can quickly find resolutions to get production back up and running.
When problems do arise, as the first order of business, a PPG team member verifies that the boxes were manufactured to the specifications for the equipment they are running on. They’ll review the equipment specifications and then, to ensure compatibility of the boxes, they’ll refer to the standards set forth by the Packaging Machine Manufacturers Institute (PMMI).
Next, they’ll observe the boxes being run through the machines. During this observational stage, the PPG technician asks the operators about any issues shown by the machine during the period of failure or underperformance. Since the operators work with the machine daily, they have invaluable insight into its operational variability by the day, the hour and even minute. If the machine is showing even the slightest performance discrepancy, the operator will know about it. This hands-on knowledge provided by the operator is critical to identifying the problem and ultimately finding a resolution.
Once PPG technicians have verified box specs and spoken with the operators, they’ll reference equipment manuals and troubleshooting guides provided by the original equipment manufacturers. PPG technicians gain a thorough understanding of the equipment and its issues before making any adjustments. They combine the facts they’ve gathered along with their hands-on experience to solve problems.
Although no two customers and their operations are alike, PPG technicians do encounter some of the same common issues, including those related to maintenance. From pressurized suction cups developing holes to adhesive buildup on parts, PPG technicians see firsthand the headaches, time and money spent when equipment is not properly maintained. They stress the importance of incorporating a routine maintenance program, where worn parts are replaced and periodic cleaning is done to avoid production problems in the future.
Another common issue PPG technicians identify has to do with improper setup and/or misalignment. Each operation, along with its equipment, has different setup procedures and requirements. PPG technicians train equipment operators on full setup procedures, including fine-tuning adjustments for varying dimensions and performance grades. By properly training operators, they help to minimize those production problems that may occur from incorrect setup.
So once an issue is identified, do PPG technicians make the quick fix and go on their way? The answer to that would be a resounding “no.” PCA’s PPG technicians aim for the long-term success of each customer. Following that ethos, PPG technicians show the customer exactly what the issue is and how to fix it. If machine problems do arise in the future, the customer’s operators know how to troubleshoot on their own and are able to impart their knowledge from the PPG to new trainees. Overall, the PPG helps minimize downtime and maximize throughput for customers’ box setup and packing operations.
Get connected with a local PCA sales rep. to learn more about how your business can increase efficiencies on your packaging line.