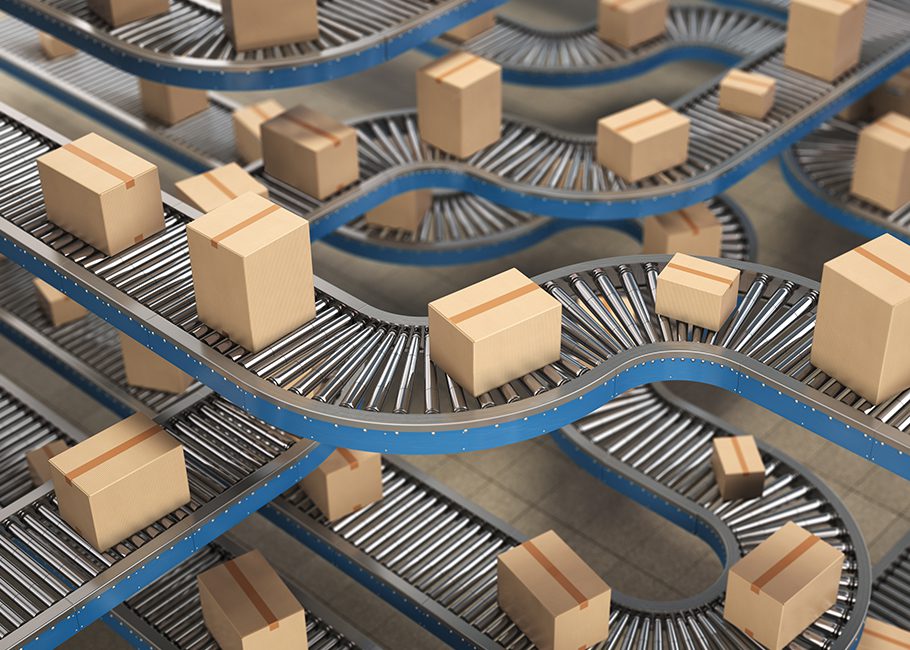
A box isn’t just a box. It can touch every part of a business’s supply chain. Underestimating its importance or relevance can lead to overlooked inefficiencies in production and distribution. The result is downtime and lost money.
PCA’s Performance Packaging Group (PPG) helps customers identify untapped efficiencies throughout their box production and distribution cycles. From troubleshooting box design to helping customers integrate new equipment, PCA’s PPG offers a broad range of services that can help increase productivity and reduce costs during multiple touchpoints in a box’s lifecycle.
The PPG delivers value to PCA customers by helping them streamline operations and optimize performance through:
- Troubleshooting Problems in Production
- Supporting New Equipment Integration
- Validating Equipment Performance
- Providing Equipment Training and Support
- Performing Comprehensive Packaging Assessments
Troubleshooting Problems in Production
When customers are struggling with boxes that aren’t running correctly on their machines, members of the PPG quickly identify the issue and implement solutions. Sometimes it’s as simple as setting up the machine correctly for box specifications or even evaluating the condition of the equipment. Either way, the PPG uses their decades of hands-on experience to find problems and get production back up and running quickly and efficiently.
Supporting New Equipment Integration
As companies continue to face pressure to do things quicker and more efficiently, the latest and greatest automation solutions continue to flood an already-saturated market. End-of-line packaging equipment is no exception. With so many options and price points available, it becomes a challenge to know where to begin the buying journey.
The PPG has years of experience in both buying and selling end-of-line packaging equipment. They have comprehensive knowledge that encompasses the industry, the products and the equipment to help customers make strategic and well-informed purchasing decisions.
Validating Equipment Performance
When companies make capital expenditures for new equipment, it’s important to validate both equipment performance and overall suitability. The PPG participates in factory acceptance tests. They’ll offer guidance on key factors, including confirming specifications and testing a correct sampling of SKUs. The PPG helps customers verify that their new equipment purchases meet the requirements and functionality necessary for their operation, reducing the risk of unexpected problems down the line.
Providing Equipment Training and Support
After integrating a new piece of equipment, companies must train their production employees on the operating procedures for the equipment. The PPG works with PCA customers on machine integration from start to finish. From making sure the equipment’s settings are fine-tuned to product specifications to training employees on setup, operation and maintenance, the PPG helps train employees on new and existing equipment.
Performing Comprehensive Packaging Assessments
Once a box has made it safely through the manufacturing cycle, it must make its way through the distribution cycle. And since every product’s journey looks different, oftentimes improvements can be made to reduce damage, save money or even simplify distribution. The PPG provides a comprehensive packaging analysis that follows the box as it leaves a local PCA box plant, goes through the customers’ facilities, arrives at the end user and reenters the corrugated recycling stream. During the assessment, PPG team members evaluate a wide range of factors and utilize the extensive resources available through PCA’s national network to identify as many cost-saving and performance improvement opportunities as possible.
If you’re ready to increase efficiencies and make bottom-line improvements, reach out to a PCA sales rep. to set up a meeting with a member of PCA’s Performance Packaging Group.