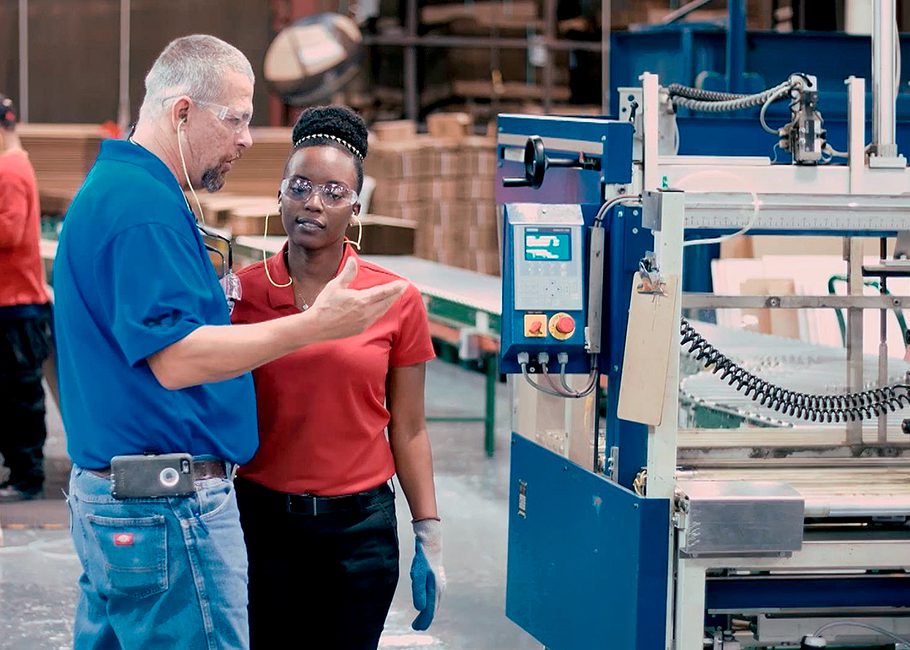
Rounding out our series on PCA’s Performance Packaging Group (PPG) is our final article on automation. If you’ve been following along in the series, you just finished learning about the importance of factory acceptance tests. Now that you’ve confirmed that your new equipment meets your standards, you are one step closer to the finish line. However, the next two steps, installation and training, are also vitally important to successful equipment integration.
For any capital expenditure project, ensuring a smooth installation process is a top priority. Installation best practices call for a detailed plan, along with a realistic timeline and schedule to help offset downtime. In your plan, you’ll want to include comprehensive checklists to ensure both the equipment and installation site meet all necessary requirements. From looking at electrical and pneumatic requirements to spatial constraints, it’s important to consider and evaluate all possible influences, including safety and compliance, to guarantee the most effective and efficient installation.
While a smooth installation process is a top priority, Randy Thompson, head of PCA’s Performance Packaging Group, strongly suggests that training has the greatest impact on future productivity. Training is key to both successful integration and long-term performance of automated packaging equipment. Thompson frequently emphasizes the importance of training to PCA customers who are integrating equipment into their operation, as he knows firsthand the impact it can have on overall productivity. According to Thompson: “The transition from setting up boxes by hand to having them machine erected is a big hurdle for workers. You’re taking machine feeders and turning them into machine operators.” As operators, employees now need to know how to diagnose, troubleshoot and maintain the equipment they run. Without the right amount and type of training, these newly minted operators will lack the tools needed to get the most out of their new packaging equipment.
So what type of training best supports equipment operators? Training can come in all shapes and sizes: including formal versus informal, high-level versus low-level, top-down versus bottom-up. However, based on several studies, it appears that training presented in a systematic manner that highlights conceptual relationships and proceeds from high-level, abstract information to lower-level, specific heuristics (or “rules of thumb”) has the strongest effects in knowledge acquisition and assimilation among manufacturing workers.1, 2 Based on this information, one option would be to start training operators on the different systems of the equipment and the interrelationships between them. After they have a basic understanding of the equipment, you can dive into the functionality and individual requirements of the separate modules, components and parts. Once your operators are brought up to speed with the right training, your packaging line’s flow rate should quickly follow suit. According to Thompson’s experience, “Every hour spent in training gets paid back exponentially in uptime of your process down the line.”
We hope that you enjoyed our series on integrating automated equipment into your packaging line and that you learned a few helpful tips in the process.
Get connected with a local PCA sales rep. to learn more about how your business can increase efficiencies on your packaging line.
Sources:
- Linou, N. and Kontogiannis, T., The Effect of Training Systemic Information on the Retention of Fault-Finding Skills in Manufacturing Industries (2004)
- Koubek, R. J., Clarkston, T. P., and Calvez, V., The Training of Knowledge Structures for Manufacturing Tasks: An Empirical Study (1994)