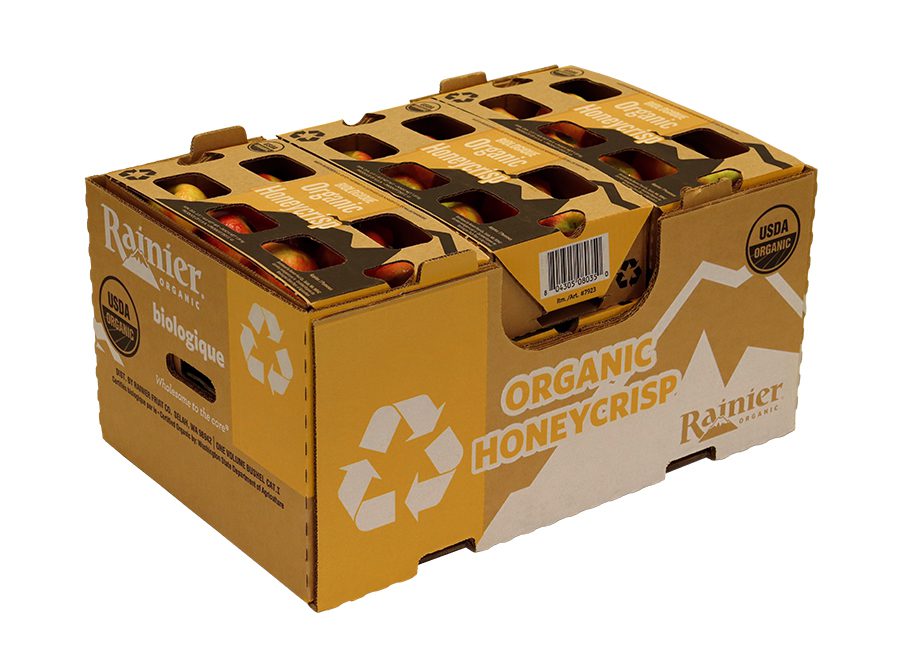
Head to the produce section of any grocery store and you’re likely to find roughly 200 different types of fruits and vegetables. From nature’s tiniest gems (blueberries) to its most robust (watermelon), each item found in the produce section has its own unique way of being grown and harvested to safeguard its viability. So once it’s grown and harvested, packaging plays a vitally important role in protection.
From farm to fork, corrugated is and always will be the smart, sustainable choice for packaging produce. Corrugated has been around for 200+ years. Its longevity can easily be attributed to its strength, its flexibility, its efficiency and its effectiveness. Corrugated is an ideal solution for produce packaging. Aside from being the most sustainable option available, here are five additional reasons corrugated is an excellent choice for produce protection.
1. Preserving Freshness Through Design
It’s time to pack the produce. From the grower to the retailer, corrugated is an ideal packaging medium to retain freshness. Different types of produce have different packaging needs. Would you package a blueberry the same way you’d package a watermelon? No. Produce isn’t one-size-fits-all, and its packaging shouldn’t be either. Packaging produce properly to mitigate damage and safeguard freshness during transportation and handling requires a packaging solution that can be customized to a product’s characteristics and transportation conditions.
Corrugated can be specially designed for individualized produce needs. It can be adapted for the shape; the size; the weight; and even the picking, packing and distribution conditions. That means it has the same potential for a pear that it does for a pumpkin. Corrugated can be manufactured to exacting tolerances for any product, helping maintain integrity from the harvest floor all the way to the retailer.
In addition to being able to be produced in various sizes, shapes and strengths, corrugated can also be made with specially ventilated designs that help preserve freshness. Vent holes enable airflow to facilitate produce’s cooling process. With corrugated, vent holes can be strategically shaped and placed to optimize cooling for specific produce characteristics.
Finally, corrugated is great at absorbing moisture, making it an ideal solution for fighting humidity. A common misconception is that it breaks down when it’s wet. If transportation or storage environments are particularly harsh, corrugated can be coated with a barrier for enhanced moisture protection and added package durability. Corrugated can even be used for hydrocooling and top-icing applications.
2. Assured Supply
The farm to fork journey can be a delicate one that relies on consistencies throughout the supply chain to ensure the best possible outcomes. However, anything from environmental factors to poor packaging can impede the process, affecting everyone’s bottom line. From an early harvest to a bumper crop, corrugated provides an assured source of supply to fit the needs of every grower and every crop, regardless of timing.
With over 1,100 box plants operating in nearly 1,000 cities and towns across the U.S., corrugated produce boxes can be purchased and replenished quickly to accommodate changing harvesting seasons and production demands. Corrugated production can be easily adapted to a grower’s demand and can accommodate supply changes quickly.
Plus, many corrugated manufacturers have stock agricultural packaging programs, where they keep a variety of commonly used containers and packaging supplies readily available or warehoused for customer convenience. From wet service to small fruit, companies like Packaging Corporation of America (PCA) have stock agricultural packaging programs that include everything to accommodate produce needs.
Corrugated is always readily available to accommodate the different growing seasons.
3. Corrugated Is Lightweight
Corrugated packaging is lightweight, but it has sufficient stacking strength to resist crushing in any environment. Plus, corrugated packaging is rightsized. Rightsized packaging means that the container is manufactured with only the materials necessary to provide the intended effect. Developing packaging for a specific produce eliminates excess material in production and waste. Corrugated reduces the amount of space a package takes up in the freight truck, allowing for more units per truckload. Corrugated loads of produce will cube out before they weigh out, meaning more fresh fruits and vegetables are being shipped per truckload.
4. Corrugated is Clean—Every Time
Corrugated offers unparalleled freshness from start to finish. Beginning with the manufacturing process, the paper used for corrugated is heated up multiple times, virtually destroying any presence of germs or bacteria.* Unlike other containers, corrugated minimizes the likelihood of foodborne contamination.
Plus, many corrugated manufacturers (including PCA) are governed and comply with the Global Food Safety Initiative (GFSI). GFSI certification is a third-party audited and universally accepted verification of a company’s systems and standards supporting food safety. For corrugated, that means the production process is regularly examined and rigorously documented, including ongoing analysis of production facilities and processes to identify hazards. And GFSI requires food safety training for all employees to ensure compliance.
5. Corrugated Is Easy to Transport
If meeting the common footprint standard is important, corrugated can meet that need as well. Uniform dimensions and stacking tabs make for efficient loading, handling and shipment of standardized pallet loads. This translates into cost savings, optimized cube utilization and load stability. Additionally, corrugated weighs far less than other packaging materials.
Learn more about PCA’s corrugated produce packaging products
*Source: Paper & Packaging, Surprisingly Interesting Facts About Your Food’s Packaging